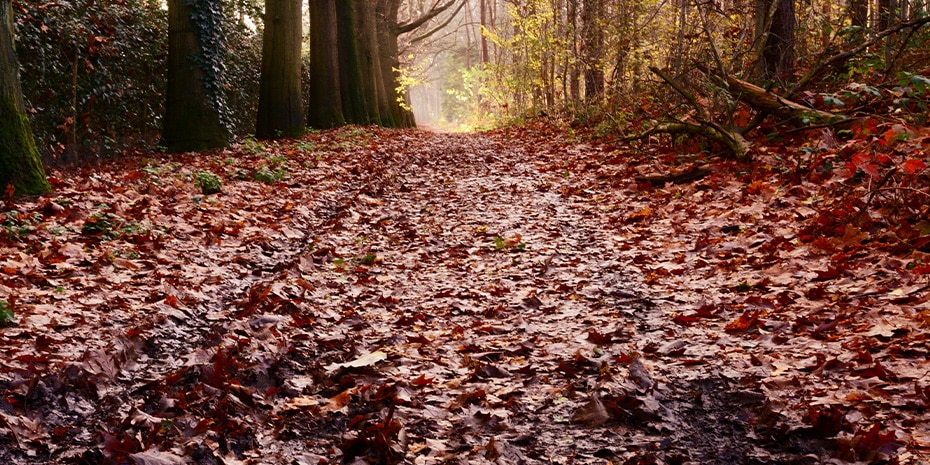
It was early October in the first year of Burkholder Buildings. I hadn’t been building sheds very long, but that day I was feeling good.
Two sheds to deliver in one day. This was an exciting first!
My twin brother was visiting from Vermont, and we left early that Saturday morning for the first delivery to Cecil Lake, some 45 minutes away. Our load was a tiny shed, 4 feet wide and 6 feet long, to be used for a power shed.
Because of its size, it was hard to load, sitting precariously on the end of the trailer. The skids were flush with the outside of the floor, so I couldn’t strap over the skids.
We wedged extra boards beside it to fill up the space between the shed and the outside of the trailer. Even so, on a hard corner a few miles down the road, the building had shifted dangerously, and we had to stop and redo our straps.
Part of our route was down a very greasy gravel road, with much more grease than gravel. Now there may be parts of the world where the mud is more treacherous than it is in Peace River country, but if so, I have not been privileged to see it.
The mud around here is famous in the memories of those who have experienced it. Our soil is high in clay—when it gets wet it turns into a heavy goo, and when it dries, it resembles concrete.
This morning it was in the gooey stage, caking onto the tires in an ever-thicker layer. But not all of it clung to the tires; plenty more was slinging through the air, until the sides of the shed were covered with mud.
Eventually, we found the customer’s place. And our first order of business was to try to wash off the muddy decorations.
The building on our trailer was not unlike a Christmas tree—tall and green, with white trimmings. It even had a red tin roof to match! It was so skinny for its height that it threatened to tip over when we were unloading it.
But at last, we were safely unloaded and on our way back home, with a stop at Tim Hortons for breakfast. Little did we realize what all we would need to use those calories for.
The second shed for the day was not one I had built, but a building I was selling on consignment for another of my customers. It was an 8 by 16-foot studio with a porch on the end, finished board-and-batten style.
Our destination this time was a hillside property with views of Charlie Lake. Beautiful setting for a home, but a difficult delivery for a shed hauler. I was so glad my brother was there to help.
The site for the shed was not easily accessed from the home driveway, so we had to back in through the neighbor’s property. And of course, there was a fence, so that had to come down.
Finally, we approached the site. But our troubles weren’t over yet. The site was very sloped, and beside it was a large poplar tree. When we backed into position, the slope pitched the building into the tree.
Now my shed trailer was a well-worn model. No independent axle lifting features or side shift for that matter.
So, what could we do? How do you lift one side of your trailer 16 inches? We studied the problem, we scratched our heads, and finally, we stacked planks on the low side.
Carefully, we backed up onto them. Carefully, very, very carefully, we eased into place. After coaxing the winch wiring to compliance, we slid the building into place.
No damage, no broken branches.
The job was done. I don’t often take the loop through Crescent Drive on the shores of Charlie Lake, but when I do, I crane my neck for a nostalgic glimpse of that memorable delivery.
May there never be a repeat!