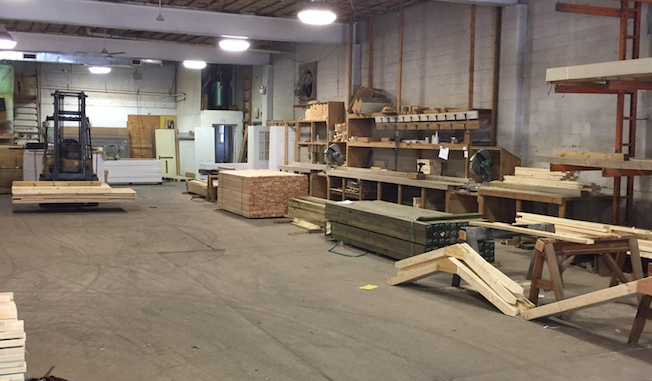
If you’re building sheds or shed components in a manufacturing facility and pay attention to your bottom line, then you’ve certainly asked at some point, “How can I build this better?”
Having set processes in place to get repeatable levels of productivity and limit waste and inactivity can go a long way in creating consistent quality structures at a predictable cost. But are your processes the best ones? Or is it just the way you’ve always built?
To answer this question, we reached out to several shed builders to discuss how they operate and why they do it the way they do. Once you start thinking about why you build the way you do, you may realize that an adjustment to your material flow or storage practices could be enough to boost your bottom line this year.
STATIONS AT THE READY
Dennis Sullivan, owner and president of American Shed Builders Inc., oversees a crew of six in an 8,000-square-foot facility in in Old Bridge, New Jersey. The facility serves as the staging ground for creating assembled components to help speed construction on the customer’s site.
“We build all our sheds at the customer’s site, so you won’t see any in progress at the shop,” Sullivan explains.
Instead, you will see materials organized against the walls and cut materials stacked for use when needed.
“We manufacture parts and pull from inventory to create the various shapes,” Sullivan says.
Having a ready inventory of stock components, not only ensures you can move quickly when an order comes through, but can also keep employees busy during slow times.
ASSEMBLY-LINE THINKING
It’s that kind of thinking about how best to be productive that has Zach Pirrello, owner of Long Island Shed Builders in Smithtown, New York, looking to reorganize his manufacturing process.
“My old landlord manufactured rolling overhead doors, and he transferred to an assembly-line process where he could put people in then cross-train them. So, if someone was sick he could take someone else and put them in that place,” Pirrello explains. “That’s what I’m trying to do. It’s more like having a person specialize in one task, but because everyone can do everything, there’s always backup. Or because we do a variety of different buildings, if someone doesn’t have work for what they specialize in, they’re able to do work on something else.”
Right now, achieving that streamlined flow depends on training young workers. Like virtually every company in the construction industry today, Pirrello is challenged to find skilled labor, so training and troubleshooting are critical to get good results. Of the five people focused on building sheds for the company, Pirrello and two others can build from beginning to end while two trainees are learning to specialize.
“Right now, everyone does everything, but we’re going to a process where two guys will build everything up to putting the building together, and then we’ll roll it forward on these carts that I made to a paint booth, spray it, then roll it out to the tents just outside the building where we’ll build the roof, the siding, windows, and doors,” Pirrello says.
SPECIALTY STATIONS
The assembly-line process has proven effective for Spanaway Sheds in Spanaway, Washington. Sales and office manager Samantha Cole explains that the company’s 10 builders each tend to specialize.
“We have a few different people who specialize in certain packages, because we offer different packages: playhouse packages, garage packages. Not everybody can do every one,” she says.
Each package flows through the manufacturing facility in specific sequencing from one station to the next.
“It’s an assembly-line structure: They get put up, then they get roofed, they get painted,” Cole explains.
Builders are trained in specific skillsets, rather than an overall approach to building. Cole notes that Spanaway Sheds doesn’t hire builders specifically for their shed knowledge, but for “a good concept for building.”
She adds, “We have had people come in who don’t have a whole lot of experience, but for the most part if they have some concept of building they’re able to do the training.”
MATERIALS ON THE MOVE
Land is pricey in Long Island, New York, so manufacturers in this region find they have to get creative to store product and materials.
Long Island Shed Builders operates out of 5,500 square feet of manufacturing space, but Pirrello quips, “We really need 15,000 square feet.”
So to create additional space, Pirrello and his team have gotten creative. The company has ¾ of an acre that includes the display lot, as well as storage. Because the manufacturing facility is limited by 14-foot ceilings, the company erected a tent outside for extra storage. They added cantilever racks purchased at auction that Perrillo, who also does metal fabrication, installed within the tent to hold fabricated shed components.
Because the company orders inventory by tractor-trailer loads, material storage space is at a premium.
“For bulk storage, like siding, we built a couple of our own buildings, 12 by 26 structures with open faces where we could just slide in boxes of siding,” Pirrello says. “Then I dropped a couple of 45-foot sea boxes—the freight containers—and we’re going to put a tent as a roof between the two containers and use them to store the overstock plywood and the lumber.”
Doors and windows remain in their containers for added protection during storage.
Of course, with this much material on-hand and in tight quarters, it helps to have tools to simplify materials and shed movement. Pirrello built a number of small carts that make it easy to maneuver the sheds. The carts sit half an inch off the floor and were built to sit around a 4 by 4. They have four spinning casters, each of which is rated to support 2,500 pounds.
“You can move up to a 10,000-pound building, and we push them around the shop,” Pirrello shares. “We can get the forklift in there, but then the building in front would be in the way. With these, we can get the building up and push them around by hand.”
This simple construction makes it possible for a single person to push an 8 by 12 shed with little effort.
“We’ve pushed up to a 12 by 26 shed in here,” Pirrello adds.
REINVENTING YOUR FLOW
While the build may look different for on-site and custom sheds, it’s crucial to have processes in place in the field or the manufacturing facility to manage the flow of shed components and material.
Some home and commercial construction companies have adopted “lean” techniques as a structured, predictable way to boost efficiency and eliminate wasted time, materials, and productivity from the construction process.
While you don’t need to reinvent the wheel to build a more productive shed building business, it may not hurt to ask “why” more often during the building process to begin imagining how you might do things better.